Enhancing Lithium Production Efficiency
The rise in the demand for electric vehicles (EVs) has led to an increased need for lithium, a crucial element in battery production. As seen by experts, there exists no viable substitute for lithium in most energy-intensive battery applications. Lithium's unique chemical properties, such as high electrochemical potential and light weight, make it the ideal material for achieving the high energy density and long cycle life required for modern batteries. As the industry grows, the challenge lies in ensuring that lithium extraction and production processes are efficient, sustainable, and capable of meeting stringent quality standards.

Challenges in Lithium Production
Currently, lithium production is predominantly sourced from two main types of deposits: spodumene (hard rock) and brine.
- Hard rock mining involves crushing spodumene ore, calcination, and leaching. The calcination step for spodumene typically involves heating the material to around 1000°C to convert it from the α-phase to a more reactive β-phase before leaching. The lithium production process is energy-intensive, and requires accurate temperature control and chemical dosing to ensure high yield and product quality together with environmentally friendly operation.
- Lithium extraction from brine traditionally uses solar evaporation to concentrate lithium from brine in large evaporation ponds. The ability to harness solar power for lithium production remains a key benefit, as it is cost effective and aligns well with global efforts to reduce carbon footprint in the supply chain.
However, the evaporation process is slow, taking between 12 to 18 months. One of the most critical issues is the massive amount of water required to extract lithium from brine. In arid and semi-arid regions where these operations often occur, this leads to depletion of scarce water resources, affecting local agriculture, ecosystems, and communities that rely on groundwater.
Advancing Lithium Extraction: Innovations for Efficiency and Sustainability
Improvements in lithium production methods are focused on increasing efficiency, improving product quality and reducing environmental impact. These on-going efforts include enhancing traditional production methods like brine evaporation and spodumene leaching processes as well as developing new technologies such as Direct Lithium Extraction (DLE).
- Direct Lithium Extraction: One of the most promising recent advances in lithium production is the DLE technology. Unlike traditional brine evaporation, DLE extracts lithium directly from brine without the need for large evaporation ponds. This method can significantly reduce water usage and extraction time. DLE is also more versatile, as it can potentially be used in a wider range of brine resources, including those with lower lithium concentrations. DLE is an emerging technology, and while promising, widespread industrial adoption is still a challenge.
- Enhanced Solar Evaporation: Traditional solar evaporation is being improved, for example, through better monitoring technologies to increase efficiency. Better monitoring of evaporation rates and chemical balances in the ponds help speeding up the process and improve the lithium yields.
- Sustainable Water Management: Given the environmental concerns surrounding water consumption, closed-loop water systems are being investigated. These systems aim to minimise water extraction from the environment by reusing water during the production process. While closed-loop systems have the potential to significantly reduce water usage, they are not yet fully adopted on a large scale in lithium production.
- Optimisation of leaching processes: Optimisation of leaching processes aims to make spodumene-based lithium extraction more sustainable and cost-effective with higher production yields and consistent product quality.
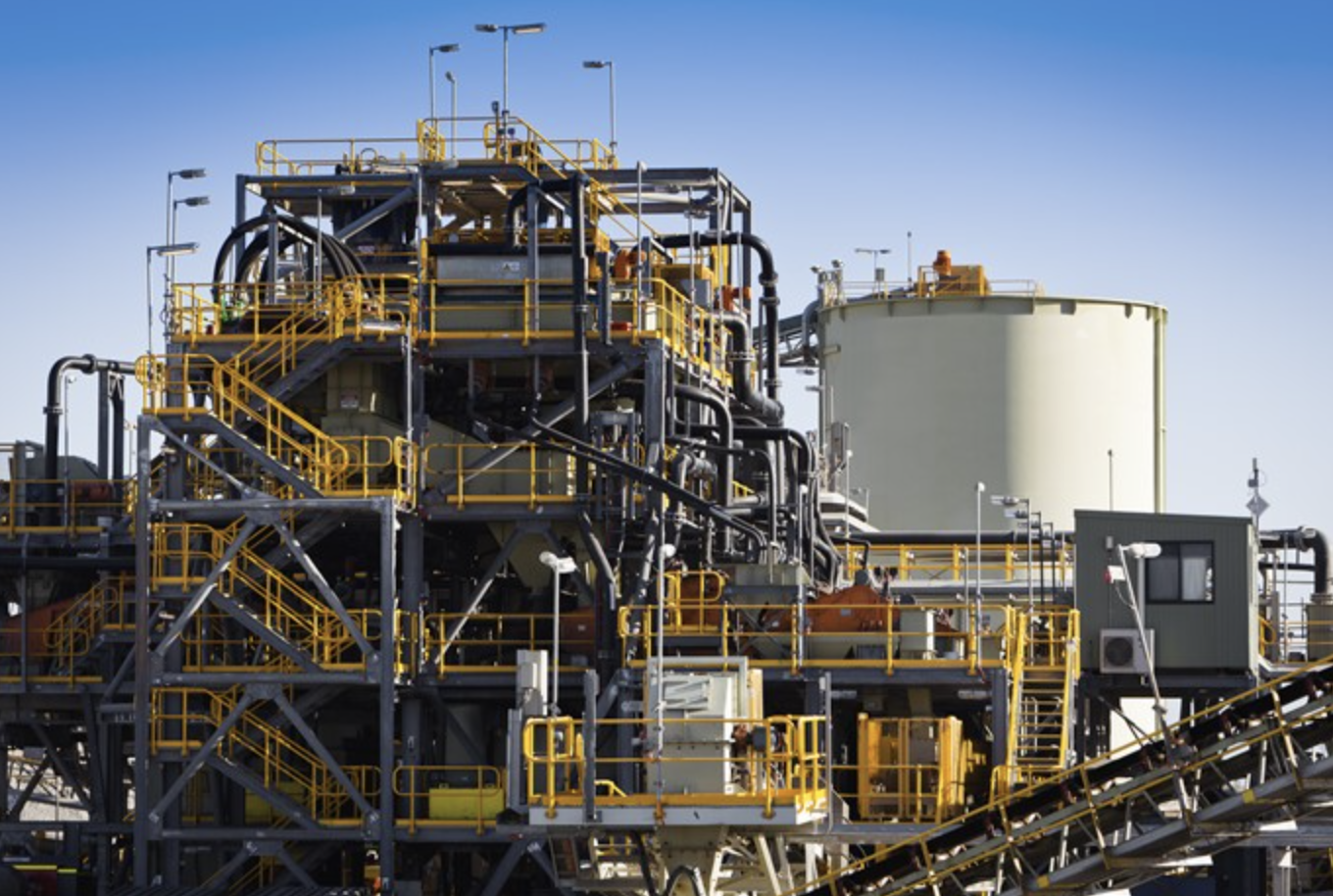
Improvement starts with measurement
Lithium production involves complex chemical processes that must be accurately monitored to ensure both efficiency and high yield. A critical aspect of this is maintaining high purity levels, as even trace impurities can drastically affect the quality and value of the lithium produced. To reach optimal processes, real-time measurement of key parameters is essential.
Traditional monitoring methods often struggle to provide immediate data, making it challenging to optimally adjust and manage the processes. By fully automated monitoring of metal concentrations in real time, operators receive immediate feedback, enabling them to make adjustments to optimise performance and prevent potential issues before they arise.
Integrating automated real-time data collection and analytics provides a deeper, more accurate understanding of the process, supports faster decision-making, and allows for more precise control. This not only leads to more efficient operations and higher productivity but also ensures sustained improvements over time, enhancing both the quality and yield of lithium production.
For efficient process control, fully automated measurement systems like Sensmet’s µDOES are essential for delivering real-time data, enabling precise adjustments, and maintaining consistent quality. Automated systems not only reduce the need for manual intervention but also enhance efficiency by instantly detecting and addressing variations in the process.

Sensmet’s μDOES Technology − The Real-Time Solution for Lithium Production Optimisation
Sensmet has developed an advanced online technology called μDOES (Micro-discharge Optical Emission Spectroscopy) that addresses the measurement challenges in lithium production. The μDOES system is designed for real-time, on-site monitoring, providing immediate and accurate quantitative data on lithium, sodium, and potassium concentrations along with impurities such as calcium and magnesium in the hydrometallurgical production processes.
How it works?
The proprietary μDOES technology creates micro-plasma within the aqueous sample using high-voltage pulses. The micro-plasma excites atoms and ions, causing them to emit light at their characteristic wavelengths. Analysis of the emission spectrum provides detailed information about the elemental composition of the sample in real time.
Advantages of Using Automated μDOES Analyser in Lithium Production
- Real-time Monitoring: Unlike traditional methods, μDOES offers continuous, real-time monitoring of lithium concentrations and impurities, enabling immediate adjustments to maintain optimal production conditions.
- High Precision and Accuracy: μDOES allows for real-time quantification of metals in the low μg/L concentration region, ensuring that even trace impurities are identified and managed effectively, comparable to the performance of traditional laboratory ICP-OES methods.
- Cost-Effective and Environmentally Friendly: The μDOES system operates without the need for harmful chemicals or carrier gases such as argon, significantly reducing the operational costs and aligning with the green chemistry principles.
- Long-term Stability: µDOES delivers consistent and reliable results, ensuring sustained accuracy over prolonged periods, which is essential for continuous industrial operations.
- Ease of Use and Flexibility: µDOES presents an automated solution for hydrometallurgical process monitoring, from liquid sampling to real-time presentation of analytical results on the end-user's DCS system. Prolonged maintenance intervals and options for multiple sampling lines support enhanced operational efficiency.
Conclusion
By addressing the needs and current challenges in lithium production through real-time monitoring, Sensmet's μDOES technology proves to be a game-changer. The innovative real-time µDOES analyser offers an advanced solution for optimising lithium purity, enhancing efficiency, and promoting sustainability in this rapidly growing industry.
Learn More About Sensmet’s μDOES Solution
- Request a Technical Brief: Understand the technical details and benefits of μDOES analyser technology.
- Download Product Brochure: Get detailed insights into how μDOES analyser can transform your lithium production processes.
- Contact Us: Reach out for personalised consultations and inquiries.
Keep up with the latest advancements in lithium production by subscribing to our newsletter or joining our LinkedIn community.
Our clients have called it a game changer
- Ensure that the black mass recycling process is optimised. Monitor the Ni, Co, Mn, and Li removal in real time. The measurement is precise, and measurement ranges are highly dynamic.
- Measure concentrations of impurity metals such as Cu, Fe, Al, Zn, Ca, Na, K, and Mg.
Additional Reading:
Breakthrough technology for battery metal production and recycling processes
