Questions we frequently hear from our customers
- How low are the µDOES® detection limits?
- How do you compare µDOES® operating costs to ICP-OES?
- How do you compare µDOES® maintenance costs to ICP-OES?
- How conductivity affects the measurement?
- Is sample dilution necessary when the conductivity of the sample falls below 10000 µS/cm?
- Is it feasible to measure a sample with a pH of 11, and can the conductivity still be adjusted by introducing acid to the mixture?
- Is it possible for the sample to contain organic components?
- What requirements must the sample meet, e.g. suspension (sediment + particle size), conductivity, salinity, pH, temperature, viscosity, chlorides, etc.?
- We plan to submit samples to your application laboratory for a feasibility assessment. Could you please provide guidance on the recommended sample volumes necessary for conducting the feasibility tests? Additionally, could you advise on the optimal and practical amount that would be
convenient for your testing processes? - What is the resolution and the spectral range measured by the µDOES (Model mD-mDOES-E-4-3)?
- What is the data format of the measured spectra?
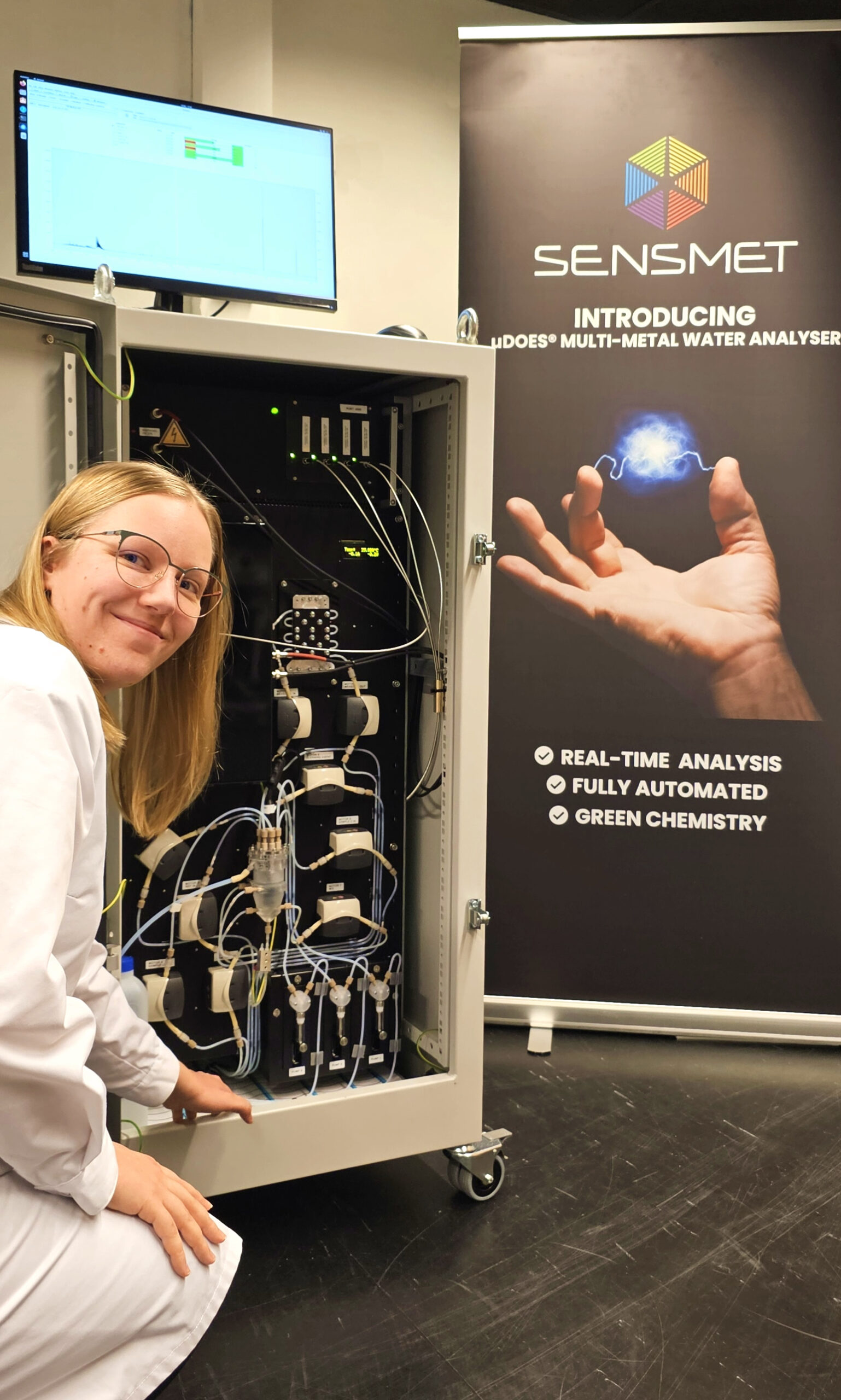

- Is the device calibrated on standards? How is the method checked?
- Is it possible to utilize an internal standard with µDOES?
- Could you elaborate on the device's chemical resistance, specifying the range of chemicals it can withstand? How about instrument contamination?
- Does the device come equipped with filters, and is there a need for regular replacements?
- What is the water consumption rate of the µDOES® system, particularly in terms of MilliQ water, and how does it vary across its different functions?
- What is the precise volume of the µDOES® cuvette, and what is the minimum quantity of diluted sample required for a measurement?
- Why is the dilution unit designed to produce a maximum of 200 ml of diluted sample, and how is this specific volume employed in the measurement process of the µDOES® analyzer?
- What specific tasks are included in the maintenance plan to ensure optimal system performance and longevity?
- What is “dark current” and how is it corrected?
- What is the “background continuum”? Is it relevant to µDOES®? If yes, how is it corrected?
- What is off-peak background correction? Is it used? If not, why?
How low are the µDOES® detection limits?
The µDOES® technology is extremely sensitive. Our capability extends to generating emission spectra at remarkably low metal concentrations found in ultrapure water of the highest grade. However, the practicality diminishes when attempting to measure nearly negligible metal concentrations in the purest water available.
In terms of practical applications, we prefer to talk about lowest quatification limits rather than detection limits. Still, the lowest quantification limits are application dependent, they depend on several factors, including
1) the composition of the sample matrix,
2) metals being analyzed,
3) the applied µDOES® measurement parameters.
With a standard µDOES® instrument, quantification limits for most battery metals typically range from sub µg/L to a few µg/L in a sample mixture where the total concentration of metal ions hover around some mg/L. In such a sample mixture, achieving µg/L accuracy is feasible. When the total concentration of metal ions increases, the lowest quatification limits also rise. The quantification limits are also influenced by the instrument parameters, which are generally fine-tuned to ensure stable and reliable results for the application rather than achieving the lowest possible limits of detection.
How do you compare µDOES® operating costs to ICP-OES?
ICP-OES manufacturers have developed indicative cost calculators, such as the one available here. As of the time of composing this response, the calculator provides an estimate for the annual operating cost of an ICP-OES, ranging from 10 000€ to 15 000€ with default parameters (8 hours of operation per day, 261 days per year, totaling 2 088 hours), encompassing electricity and carrier gas expenses.
In 2023, a Sensmet customer in Germany, who owns an ICP-OES, calculated their argon cost at 10€ per hour (960 hours annually, resulting in an approximate yearly argon cost of 10 000€). Meanwhile, another customer in Finland revealed that their laboratory incurs an annual expenditure of 100 000€ on liquid argon. However, they noted that this cost would soar to 450 000€ per year if they opted for gas cylinders instead of liquid argon, considering the use of six ICP-OES instruments operating in two shifts.
While µDOES® does not require argon, it necessitates high-quality demineralized water to dilute samples. In Sensmet's laboratory, MilliQ water costs approximately 0.3€ per liter, with a typical hourly consumption of 2 liters. Furthermore, in comparison with ICP, µDOES® exhibits lower electricity consumption, amounting to less than 15% of the typical electricity usage of an ICP (less than 300W vs 2000W).
Drawing from these examples, the running costs associated with argon and electricity for an ICP-OES instrument fluctuate between 5€ and 15€ per hour, excluding consumables and maintenance expenses. The comparable µDOES® cost is ca 0,5€ - 1€ per hour, excluding consumables and maintenance expenses.
How do you compare µDOES® maintenance costs to ICP-OES?
If operated continuously around the clock, the µDOES® requires electrode replacements every six months and pump replacements annually. The cost of consumables typically falls in the range of 5 000€ per year, as per Sensmet's price list in the EU.
For comparison, in 2023, a Sensmet customer in Germany who owns an ICP-OES calculated their maintenance costs with a recorded annual usage of 960 hours:
- Maintenance is predominantly conducted by the customer’s in-house staff, requiring approximately 50 hours per year (including cleaning of the quarz components)
- The customer’s expenditure on consumables and spare parts amounts to approximately 5 000€ per year
- Additionally, the customer orders yearly maintenance from the vendor, incurring a cost of around 3 000€ per year
- According to the customer, it's customary for us to invest an additional 10 000€ - 20 000€ in repairs every five years. “This year, an unforeseen issue arose as the frequency generator failed.”
Another customer owning ICP-OES stated that their yearly cost for consumables is typically 8 000€. He continued that the “costs are moderate, and OES runs stably because nobody can afford a dirty sample introduction".
A German expert concluded: “The most signicant advantage of µDOES® is the 24/7 measurements without the need for laboratory staff, directly at the process plant under relatively harsh conditions. The maintenance costs of an ICP or µDOES® are both irrelevant because they generate far more profit overall.
How conductivity affects the measurement?
The strength and size of the plasma are inversely proportional to conductivity levels; lower conductivity yields a stronger and larger plasma, while higher conductivity results in a weaker plasma.
In instances where conductivity surpasses a certain threshold, plasma ignition may not occur. This critical point, typically falling within the range of 10000 to 20000 µS/cm, depends on applied current and energy parameters.
To achieve optimal performance for a specific application, it's essential to maintain the selected conductivity level constant during measurements. For instance, one may set the conductivity to a specific value, like 5000 µS/cm, and consistently adjust the conductivity by adding a controlled amount of acid to the diluted sample. This meticulous approach ensures stable and reliable measurements.
Is sample dilution necessary when the conductivity of the sample falls below 10000 µS/cm?
Indeed, dilution is a necessary step, with the primary aim being to optimize the concentration of cations rather than solely diminishing conductivity. Usually, the dilution process brings the conductivity down to levels below 1000 µS/cm. Following this, the conductivity is then elevated to the predetermined value by carefully introducing acid into the diluted sample.
Is it feasible to measure a sample with a pH of 11, and can the conductivity still be adjusted by introducing acid to the mixture?
Absolutely, it is possible to measure samples with a pH of 11 using µDOES®. To adjust the conductivity, acid is carefully added to the sample following a substantial dilution process. The dilution is significant enough to ensure that adding small amounts of acid to the solution poses no risk.
Is it possible for the sample to contain organic components?
Certainly, the sample is permitted to contain organic components. The essential requirement is that the sample must be suitable for dilution with demineralized water. Following dilution, the conductivity can be precisely adjusted to the desired level by incorporating acid into the mixture.
What requirements must the sample meet, e.g. suspension (sediment + particle size), conductivity, salinity, pH, temperature, viscosity, chlorides, etc.?
- Suspension (sediment + particle size):
Small particles (<ca 150 µm) in moderate quantities generally do not interfere with measurements, as they smoothly flow through the instrument. However, high particle quantity, large particles, or significant sediment build-up can impact sampling system engineering, necessitating solutions like clarifiers, water cyclones, compressors for clogging prevention, and filtration.
- Conductivity:
Dilution is employed, and conductivity is subsequently adjusted to a predetermined value before measurement. Conductivity of the sample itself does not pose a concern.
- Salinity:
High salinity has a significant impact on the required dilution, consequently affecting the lowest measurable concentrations of target metals. High salinity applications may require application development to select measurement parameters that deliver optimum performance.
- Sample pH:
Direct Influence: None.
Possible Indirect Effects: pH may indirectly affect a) dissolved metal concentrations, b) oxidation states of ions, and c) complex formations of ions.
- Sample Temperature:
Heated lines can be applied before dilution unit.
After the dilution, the instrument regulates the diluted sample's temperature and measures it at a constant value.
- Viscosity:
Sampling and dilution procedures cannot be executed if the viscosity deviates significantly from the typical characteristics of water.
- Chlorides:
Effects: No significant impact.
- Matrix Composition:
If the matrix is relatively simple, containing only the listed battery metals and typical salts, there is a good chance that the application can be successfully executed.
If the sample is a cocktail of all possible metals in high concentrations and the target metals are present in very small concentrations only, it is possible that the calibration could become too complicated, and we could not compensate for interferences. Additional attention is required in such scenarios.
We plan to submit samples to your application laboratory for a feasibility assessment. Could you please provide guidance on the recommended sample volumes necessary for conducting the feasibility tests? Additionally, could you advise on the optimal and practical amount that would be convenient for your testing processes?
A convenient and commonly applicable approach is to send us sample bottles ranging from 0,5 to 1 liter for our feasibility assessment. This volume is typically relevant, feasible, and practical for most cases.
However, we also acknowledge that certain situations may pose limitations, either due to the scarcity or high cost of the sample, or an increased demand for testing. In such instances, where limitations exist, we can tailor our test plans accordingly. Even a few milliliters may prove sufficient for a successful feasibility test.
In cases where the sample material supply presents no limitations, the following guidelines outline convenient sample amounts:
- The analyzer's sample intake for diluted samples is 60 ml per measurement. Given the analyzer's fully automatic nature, we can efficiently conduct hundreds of individual or repeated measurements during a feasibility check. The consumption would be up to 50 to 100 liters of diluted sample, depending on the planned experiments. Hence, for manual dilution, the recommended minimum quantities vary based on the needed dilution ratio:
o 1:5000 or higher: 0,1 l
o 1:1000: 0,5 l
o 1:500: 1 l
o 1:100: 5 l
o No dilution: preferrably at least 30 l. - If the experiment involves an automatic dilution unit, a 1-liter sample is adequate for over 100 measured samples. This corresponds to approximately a 24-hour test sequence with a 15-minute measurement interval. In the case of using the original concentration sample, a 5-liter volume allows continuous testing the dilution unit for several days with fully automated measurements.
We remain flexible and are open to accommodating unique circumstances, ensuring the feasibility study aligns with your specific requirements.
What is the resolution and the spectral range measured by the µDOES (Model mD-mDOES-E-4-3)?
The standard µDOES (Model mD-mDOES-E-4-3) is equipped with 4 spectrometers, collectively encompassing the spectral range from approximately 200 nm to 840 nm. Each of these spectrometers features a 4k CMOS sensor, ensuring high-quality data acquisition. Consequently, every individual measurement captures a spectrum containing over 16,000 data points. With a data point spacing of around 0.05 nm and an optical resolution of approximately 0.1 nm, the µDOES delivers precise and detailed spectrum for elemental analysis.
What is the data format of the measured spectra?
By default, Senmet uses JCAMP-DX (Joint Committee on Atomic and Molecular Physical Data - Data Exchange) file format. More information of the JCAMP-DX standard can be found on IUPAC’s web page: https://iupac.org/what-we-do/digital-standards/JCAMP-DX/
The main benefits of the JCAM-DX data format are:
- The JCAMP-DX files are plain-text ASCII files, making them easily accessible and human-readable. This accessibility facilitates data sharing, archiving, and analysis, even with basic text editors or scripting languages.
- The JCAMP-DX allows for the inclusion of various metadata, such as instrument parameters, sample information, and experimental conditions, providing context and enhancing the interpretability of spectroscopic data.
- The JCAMP-DX files are platform-independent and self-descriptive, which facilitates long-term data preservation and archival. By encapsulating data and metadata within a single file, JCAMP-DX helps maintain data integrity and accessibility over time.
- The JCAMP-DX data format promotes interoperability, accessibility, and standardization in spectroscopic data exchange, facilitating efficient data sharing, analysis, and archiving.
Is the device calibrated on standards? How is the method checked?
The factory calibrations are conducted using readily available ICP-OES standards. Additionally, during the factory calibration process, we create mixtures of standards and customer samples to account for potential cross-interference effects.
Additionally, we recommend that the customers verify the instruments performance by measuring QC (Quality Control) samples. These QC samples can be measured automatically for convenience.
Could you elaborate on the device's chemical resistance, specifying the range of chemicals it can withstand? How about instrument contamination?
The device predominantly utilizes PTFE as its primary material, ensuring robust chemical resistance across a broad spectrum. Consequently, we are confident in its ability to withstand various chemical exposures.
In cases where the instrument faces substantial contamination from metals, our approach involves effective cleaning solutions, such as a 5% HNO3 solution.
Should these measures prove insufficient, our design facilitates easy tubing replacement by the customer, offering a practical solution to address and mitigate potential from contamination. It's worth noting that in applications where the sample is strongly diluted, tubing replacement is typically unnecessary.
Does the device come equipped with filters, and is there a need for regular replacements?
If the sample is essentially particle free, but there is an occacional chance for large particles, preceding the analyzer, we recommend the incorporation of a safety filter with a 200µm specification, constructed from PTFE.
If the sample exhibits particles, solids or debris, the sampling system must be designed accordingly, considering the quantity of solids or particles present in the sample. Depending on the application, an effective water cyclone, clarifier, and/or filtration process may be needed.
What is the water consumption rate of the µDOES® system, particularly in terms of MilliQ water, and how does it vary across its different functions?
The water consumption of the µDOES® system is influenced by various factors related to its operations. Let's break down the water usage in different scenarios:
Dilution:
The water used in dilution significantly contributes to the overall water consumption. The automatic dilution unit utilizes MilliQ water for dilution purposes, and the water requirement depends on the dilution ratio or the number of dilution cycles. For a single dilution cycle, the maximum dilution ratio is approximately 1:50, requiring 200 ml of water. With two dilution cycles, the ratio extends to about 1:2500, utilizing 400 ml. If three dilution cycles are performed, a maximum dilution ratio of around 1:125 000 is achieved with 600 ml of water.
For example, if the sample dilution ratio is 1:50 000 and the analyzer measures 4 diluted samples per hour (with a 15-minute sample interval), the daily water consumption would be approximately 60 liters (0.6 liters/sample * 4 samples/h * 24 h).
Reference measurement:
Conducting a reference measurement requires approximately 0.15 liters of water per measurement. Notably, the reference measurement does not contribute to an increase in overall water consumption. This is because any reference measurement is typically conducted in lieu of a sample measurement, which would typically necessitate a higher volume of water.
Sample system cleaning:
Certain sampling systems may require regular washing cycles using water. The water needed for cleaning the sampling system is additional to the quantities mentioned above and depends on the specific requirements of the cleaning process.
What is the precise volume of the µDOES® cuvette, and what is the minimum quantity of diluted sample required for a measurement?
The µDOES® cuvette has a volume of 5 ml. However, to limit the swift temperature rise caused by plasma generation during measurements, the sample intake is elevated, and the sample undergoes a continuous circulation process through a heat exchanger. To reach optimum accuracy and facilitate effective temperature control, the overall sample intake of the µDOES® analyzer is designed to accommodate approximately 60 ml of the diluted sample.
The dilution unit is purposefully engineered to generate a maximum of 200 ml of diluted sample, contributing to the efficiency of the µDOES® analyzer's measurement process. In a typical measurement cycle, the diluted sample serves two crucial purposes:
- Initially, prior to the measurement phase, the diluted sample is employed to perform a thorough rinse of the sample line, cuvette, and all wetted surfaces within the µDOES® analyzer. This rinsing process, followed by draining the diluted sample, aims to eliminate any residual sample residues or impurities, thereby enhancing response times. For the sake of precision, this rinsing procedure can be repeated as necessary.
After the rinse, an additional quantity of the diluted sample is introduced into the µDOES® analyzer for the actual measurement. Depending on the specifics of the rinsing procedure, there remains enough diluted sample to facilitate a minimum of two independent measurements, ensuring the robustness and reliability of the analytical process.
What specific tasks are included in the maintenance plan to ensure optimal system performance and longevity?
The maintenance plan comprises several crucial elements to designed to uphold the system's efficiency and durability:
- Visual Inspection: Our customers are encouraged to conduct a weekly visual inspection to identify any visible issues or abnormalities. This good practice involves checking crucial elements such as the presence of QC samples, MilliQ, conductivity agent, ensuring a flawless continuous operation.
- Peristaltic Pump Tubing Replacement: It is advised to replace the Marprene tubes used in peristaltic pumps every three months to prevent potential leakages, contributing to the overall reliability of the system.
- Electrode Replacement: To ensure continuous operation, the replacement of electrodes is recommended every six months, maintaining reliable functionality.
- Annual Maintenance: A comprehensive yearly check-up and servicing to address any potential issues, ensuring the overall health and longevity of the system.
What is “dark current” and how is it corrected?
Dark current refers to the electrical current that flows through a detector in the absence of any incident light. It is an inherent property of most detectors used in spectroscopic instruments. Dark current arises due to thermal energy within the detector material, which generates electron-hole pairs and leads to a small current flow. Hence, it adds a baseline signal to the detector output, even when no light is being detected. Unless corrected, this baseline signal can interfere with the accurate measurement of the emission signal from the sample, reducing the sensitivity and dynamic range of the instrument.
Before any sample measurement, the µDOES® performs a dark current measurement – that is, all spectrometers measure a full spectrum with no light input to the detector. This measurement provides a baseline reference for the dark current signal. During subsequent measurements with plasma ignited, the dark current signal is subtracted from the total signal to correct for its contribution.
What is the “background continuum”? Is it relevant to µDOES®? If yes, how is it corrected?
In the context of Inductively Coupled Plasma Optical Emission Spectroscopy (ICP-OES), the background continuum refers to the continuous emission of light across a broad range of wavelengths. This continuum emission arises typically mainly from:
- from the argon plasma
- spectral features from the sample matrix or contaminants
- instrumental noise and artefacts.
The plasma generation process in µDOES® (Micro-Discharge Optical Emission Spectroscopy) diverges from that of ICP-OES. Unlike ICP-OES, which utilizes argon, µDOES® does not involve the use of argon gas. Instead, the emission spectrum in µDOES® is solely derived from the ions and atoms present in the sample matrix and the electrode material. As a result, a spectrum obtained through µDOES® typically appears as a straight line from which emission peaks rise. Consequently, baseline correction is extremely simple, comprising automatic constant and, if necessary, slope corrections.
One of the most unique and distinguishing features of the µDOES® instrument is its capability for spectral interference correction. Apart from the discrete emission lines from the analyte elements, there may be additional spectral features from the sample matrix or contaminants that contribute to a continuous background signal. Through the utilization of advanced algorithms, the µDOES® generates mathematically an identical spectrum to the measured emission spectrum, incorporating all emission lines originating from the electrodes and calibrated elements within the sample matrix. This approach empowers the µDOES® to achieve quantitative results with exceptional analytical performance. Essentially, the residual spectrum contains only noise.
Is it possible to utilize an internal standard with µDOES?
Yes, an internal standard can be utilized with µDOES (Micro-Discharge Optical Emission Spectroscopy) to improve the precision and accuracy if necessary. If applied, an internal standard element is automatically added to the sample before each measurement in a known concentration. The intensity of the analyte signal is then divided by the intensity of the internal standard signal to correct for possible background effects or instrumental drift.
By measuring the intensity of both the analyte and internal standard lines, the variations in the instrumental response, such as fluctuations in plasma conditions or matrix effects, can be normalized. This normalization can help improve the precision, reliability and robustness of the analytical results.
While there is an option to use an internal standard, it's not always employed. Certain applications may not derive substantial benefits from the increased accuracy. However, in some applications, like those with unusual conditions, using an internal standard might be necessary.
What is off-peak background correction? Is it used? If not, why?
Off-peak background correction is a technique used in spectroscopic analysis to correct for background signals that arise near the analyte emission lines but do not originate from the analyte itself.
The principle behind off-peak background correction involves measuring the intensity of the background signal at wavelengths adjacent to, or "off-peak" from, the analyte emission lines. These off-peak wavelengths are selected to be free from interference by the analyte or other spectral lines of interest. By measuring the background signal at these off-peak wavelengths, one can estimate and subsequently subtract the background contribution from the analyte signal.
In the early days, Sensmet applied off-peak background correction methods. However, the off-peak algorithms are highly sensitive to spectral interference, and these were substituted by far more powerful analytical algorithms developed by Sensmet.